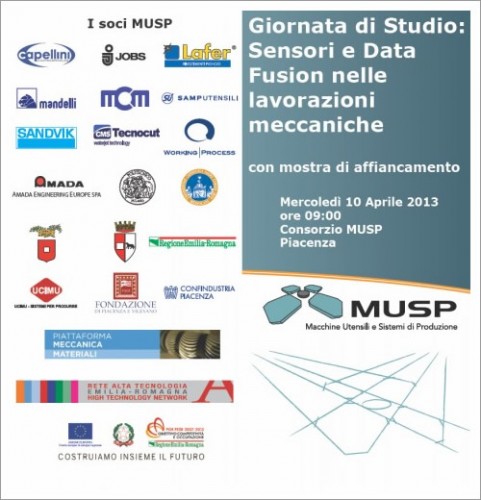
Il convegno con mostra di affiancamento, che si terrà il prossimo 10 aprile presso la sede del Consorzio MUSP, sarà dedicato a tutti gli aspetti legati alla sensorializzazione delle lavorazioni meccaniche e interesserà quindi sia i produttori sia gli utilizzatori delle macchine.
Il settore delle macchine utensili e, più in generale, delle macchine automatiche ha avuto uno sviluppo di tipo incrementale basato, in gran parte, sull’utilizzo dell’elettronica di potenza, del motion control, dello sviluppo di sistemi CNC oltre che sulla revisione e affinamento dei componenti meccanici e sull’ utilizzo di nuovi materiali. In particolare, i maggiori progressi registrati negli ultimi anni sono stati legati ai nuovi motori, brushless e lineari, ai nuovi CNC ad alte prestazioni, ai nuovi software di comando, controllo e ottimizzazione oltre al progresso nei sistemi CAE di supporto alla progettazione, calcoli strutturali elastodinamici e sistemi di simulazione software.
Sembra difficile che questi filoni di innovazione riescano a riprodursi nei prossimi anni e si può stimare che, nel complesso, il settore delle macchie utensili continui la attuale fase di “maturità” caratterizzata da sempre maggiore difficoltà di realizzare significative innovazioni. A fronte di questa crescente difficoltà di innovazione sulle orme del passato sembra aprirsi adesso la possibilità di avviare un nuovo ciclo di innovazione basato sulla loro sensorializzazione e autocontrollo. Si tratta di una innovazione del filone della così detta “smart factory” caratterizzata principalmente dalla caratteristica del sistema produttivo di adattarsi alle condizioni variabili in modo proattivo cioè di rilevare e prevenire qualsiasi anomalia o problema si presenti durante le lavorazioni. Questo nuovo ciclo di innovazione, si può prevedere, sarà basato sull’utilizzo diffuso di ogni tipo di sensori. L’innovazione consisterà sia nello sviluppo di nuovi sensori, nell’utilizzo di sensori esistenti e, soprattutto, nell’impiego e sfruttamento avanzato ed integrato delle misure effettuate.
Questo nuovo ciclo di innovazione perseguirà quindi diversi obiettivi quali:
- migliorare l’affidabilità delle macchine con sistemi di diagnostica avanzata
- migliorare la “robustezza” dei processi con sistemi di compensazione di ogni tipo di “disturbi”
- ridurre la difettosità con un controllo innovativo del processo di lavorazione
- ridurre la necessità di presenza umana.
Negli ultimi anni sono stati sviluppati e commercializzati numerosi nuovi sensori capaci di realizzare, in ambiente industriale, misure di numerose grandezze quali vibrazioni, forze, momenti torcenti, correnti, potenze, posizioni nello spazio con metodi non contact.
L’utilizzo di questi sensori on line, installati nelle macchine in funzionamento industriale, permette di realizzare funzioni di controllo, ottimizzazione, diagnosi preventiva che permettono significativi progressi nella qualità del prodotto e nella efficienza produttiva nel suo complesso. Inoltre si stanno rendendo disponibili sistemi di generazione locale dell’energia, la così detta Energy harvesting, di trasmissione senza fili e di telecontrollo via web che, accoppiati ai sensori, permetteranno di realizzare misure su parti in movimento e da posti di controllo remoti. Ma queste tecnologie, come sempre succede nei periodi iniziali di disponibilità, sono di non facile utilizzo: infatti la facilità di raccogliere grandi moli di dati on line si scontra con la difficoltà di trattarli e, soprattutto, interpretarli per ottener indicazioni facilmente utilizzabili in produzione. In particolare la presenza di numerosi sensori diversi tra loro permette di rilevare situazioni che un singolo sensore non potrebbe rilevare.
Per risolvere questi problemi i ricercatori e le aziende più avanzate stanno mettendo a punto metodi ed algoritmi di DATA FUSION che permettono, anche in tempo reale, di estrarre informazioni che non sarebbero rilevabili con misure singole. Data fusion significa infatti rilevare situazioni anomale dalla lettura e correlazione di più sensori diversi un po’ come fa il medico quando diagnostica una malattia facendoti due domande separate e non accontentasi di una sola misura. La figura riporta le coppie di misure di corrente del mandrino e di forza applicata al pezzo per diverse condizioni dell’utensile: mentre le due misure prese singolarmente non avrebbero grande significato la loro rappresentazione contemporanea permette di evidenziare bene le condizioni dell’utensile se scheggiato, usurato o in funzionamento nominale “come nuovo”.
Il futuro massiccio impiego dei sensori apre quindi la porta ad una nuova fase della meccatronica che dopo decenni di focalizzazione sugli aspetti del MOTION CONTROL sarà basata sempre più sull’utilizzo di sistemi di sensori.
L’utilizzazione efficace dei nuovi sensori richiede un approccio multidisciplinare con la collaborazione di diversi attori quali:
- gli utilizzatori di macchine utensili, frese, rettifiche, presse
- i costruttori di macchine
- i costruttori di sistemi elettronici CNC
- i costruttori di sensori
- i ricercatori e sviluppatori di sistemi di misura
- i ricercato e sviluppatori di sistemi di raccolta dati , analisi, data fusion, interpretazione
Il convegno, insieme alla mostra di affiancamento, non presenterà solo le offerte del mercato e le ultime ricerche nel settore ma, attraverso le testimonianze di utenti, metterà in risalto le richieste dei costruttori ed utilizzatori di macchine utensili per formare un quadro completo sia dello stato attuale dell’arte sia delle tendenze ed evoluzioni future.
Allegato | Dimensione |
---|---|
Invito sensori | 624.19 KB |